Coosa Panels consist of high-density polyurethane foam reinforced with layers of fibreglass. The no-rot and light-weight advantages of high-density foam combined with the structural properties of fiberglass make Coosa panels an excellent replacement for wood and other traditional core materials.
Manufactured in the USA, Coosa Panels are used internationally throughout the marine, industrial and transportation industries in structural and non-structural applications. They offer resilience and endurance, are light weight and not subject to water, rot or insect infestation.
Dimensionally stable, they are available in a variety of densities and thicknesses, boast low water absorption and do not attract mould and fungus that destroy wood.
In the marine sector, Coosa Panels meet the most demanding requirements for structural and aesthetic components in a variety of craft including pleasure craft and commercial and military vessels.
Coosa Bluewater Panels are a high density, closed-cell polyurethane foam reinforced with woven roving and continuous strand fiberglass.
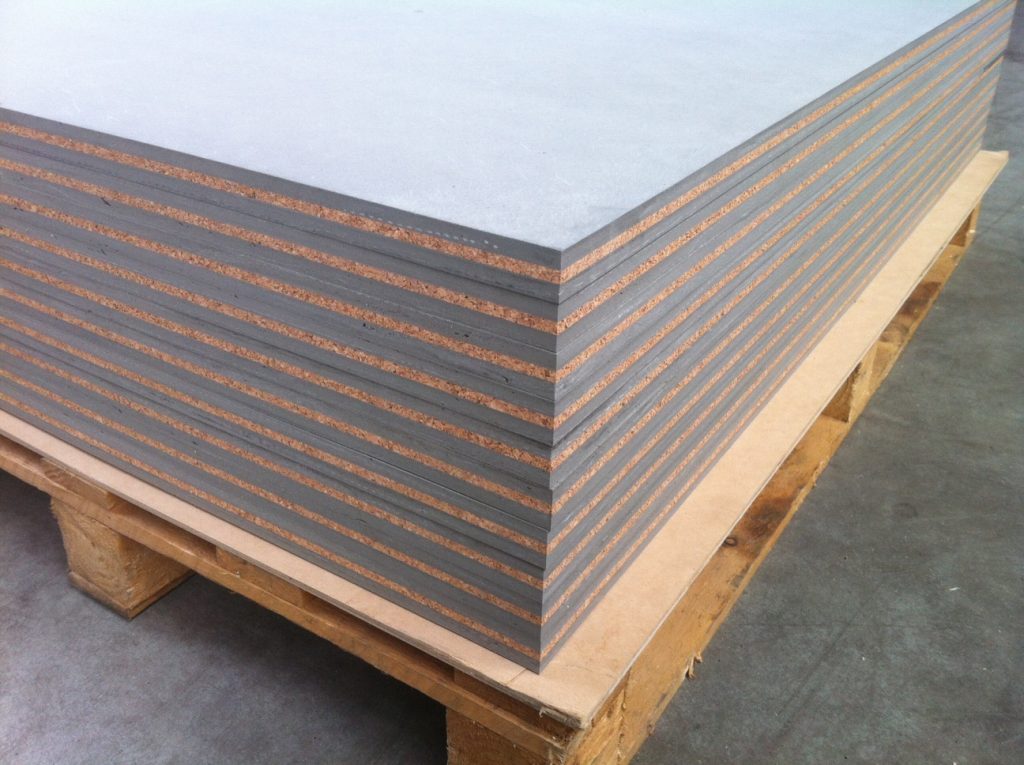
The woven roving fiberglass in addition to continuous strand fiberglass in Bluewater Panels adds additional flexural strength (stiffness) for demanding applications where structural integrity and/or greater span lengths are appropriate.
Bluewater Panels are approximately 40 to 60 percent lighter than plywood, depending upon density ordered, and offer a very low water absorption, 1.5 percent or less, therefore there is no significant weight gain when exposed to water.
The panels can be utilised for multiple applications – transoms, stringers, hatch lids and decking.
Among the many Australian boat builders to rely on Coosa Panels in numerous projects is Noosa Marine, based on Queensland’s Sunshine Coast. Director, Julian Griffiths explains that he has specified Coosa Panels for the past four years in projects as diverse as the Roger Hill-designed 19-metre power catamaran, “Bajaca” and the ultra-fast, 19.5-metre Schionning G-Force 2000 Speciale, “Kato”.
“We have chosen Coosa Panels for pieces that need to be bolted or screwed, such as decks and transoms,” he says. “It’s a high-density core that doesn’t rot or compress. You can bolt right through it, and because condensation or water can get under floors, Coosa is great to use in floors.”
For repairing smaller vessels, Julian and his team use Coosa in place of plywood.
“The advantage is Coosa has a superior rigidity at a fraction of the weight of plywood and we don’t have to fibreglass the underneath or top. We can tape it in, so we’re also saving on time as well as making the job easier.”
ATL Composites Australia and vdL Composites in Germany have also incorporated DuFLEX Coosa-cored panels into the DuFLEX Composite Panel range to offer customers a choice of pre-laminated panels, through to CNC-routed kits, for specific applications like stringers in marine applications. The CNC Kits reduce waste and labour in these projects.
More at
https://news.atlcomposites.com.au/coosa-delivers-strength-and-longevity/
For more information visit:
http://atlcomposites.com.au/products/category/30/Coosa-