Like building anything, a house, a fence, a car or a boat, considerable thought is given to the materials used for the purpose of the build. It is one of the first considerations when matching objectives with budgets and time.
Emirates Team New Zealand’s Wind Powered Land Speed project is exactly the same, as Mechanical engineer Tim Meldrum explains, “In the design process when we’re trying to determine just how we’re going to build all of these parts, the build team plays a major role, sitting around a table, thrashing out just what the process will be.”
The build team are the ETNZ boat building team based in its production facility on Auckland North Shore, a mix of young apprentices through to some of the most experienced boat builders in the New Zealand marine industry.
They know all there is to know about the materials used in their trade, and when it comes to composites, the main two options of construction are a pre-impregnated carbon fibre and dry fibre with a wet laminate.
“As the name suggests, pre-preg is carbon fibre pre-impregnated with resin,” boat builder Kurt Riechelmann explained.
“We would usually use pre-preg because you get perfect resin ratios out of it and it is not until it gets hot that the resin will flow and it’s almost like laying down dura-seal, or something like that.”
However ‘pre-preg’ does not come cheap so you need to consider the costs and weight ramifications- like when weight savings are imperative in a foiling AC75 that needs to be as light as possible to take flight.
ETNZ builds its AC75 hulls from pre-preg, since a small saving over a larger area like a boat hull can add up a lot of weight. It also allows the team to hit strict weight limits in the AC75 class rule, a lighter hull structure gives you more freedom to develop systems within the hull weight limit.
In the case of the land speed yacht, the pre-preg composites are reserved exclusively for what’s in the air above the craft; but why?
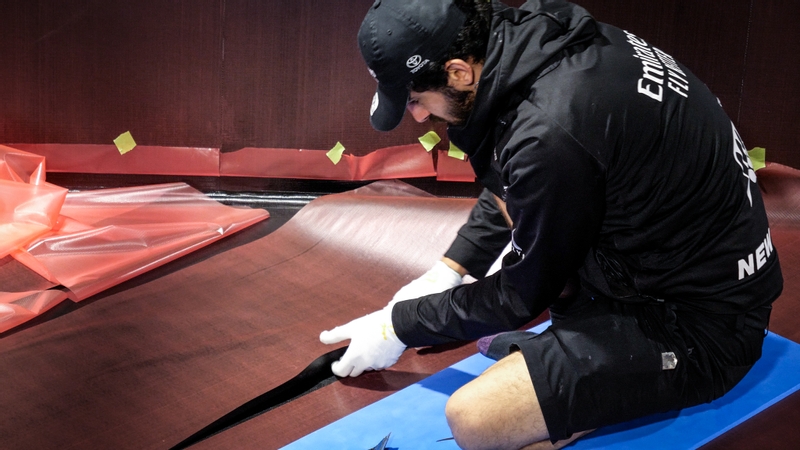
“We can be a bit more focused where we push the tech, so the mast, the wing, the spar, if we make that heavy it steals the righting moment and the stability that you need to generate power. So we are more weight conscious,” Meldrum explained.
But in the case of the main fuselage body?
“We will be adding some ballast for downforce grip in the main body so it is much less sensitive to weight than the wing. Therefore, with the land speed record craft the body is less mass critical, the weight is down low and does not affect righting moment too much.
So, pre-preg does not justify itself in this case so the smarter move is to save the time and money so we use dry fibre infusion and wet laminate.”
Some of the main body elements lend themselves nicely to the infusion process where multiple layers of carbon are placed carefully in a mould dry, then a vacuum created within a bag and resin is released to flow into the carbon and cure as a rigid part.
This process is great for thicker laminates without core and because the laminating process is done dry, it is not time pressured with resin curing.
Dry carbon fibre infusion is still a high tech material and process if you compare it to the likes of a production trailer boat.
For the production team it is a more user friendly and speedier option than pre-preg in the construction. Estimates being that it would take a quarter of the time to lay up the body of the land speed craft as it would with pre-preg.
However, because it is slightly heavier way of laminating carbon, it is much harder to achieve the optimum resin to fibre ratio, so you end up carrying a little extra resin that you don’t need in theory.
In other words, the devil is in the detail and there are margins for error, but having the experience and knowledge of how to carefully set up the infusion process can be the difference between success or disaster in the production.
“It’s a bit of a dark art, infusion,” veteran ETNZ boat builder Peter ‘Pee Wee’ Ockleston said.
“It can go wrong, and it can seriously go wrong, but the processes that we’ve been working on over the last 15 years or so, we’ve got it pretty close to getting right every time.”
It is this talent and knowledge that the whole team relies on in the ETNZ production facility that is a hidden secret to success for many of the syndicate’s production projects.
“It’s nice to have a real depth of experience within our build team so we can draw upon all forms of manufacture. We really can pick the process that best suits the part no matter what it is,” Meldrum concluded.
ETNZ